Unit 8 Robot Safety
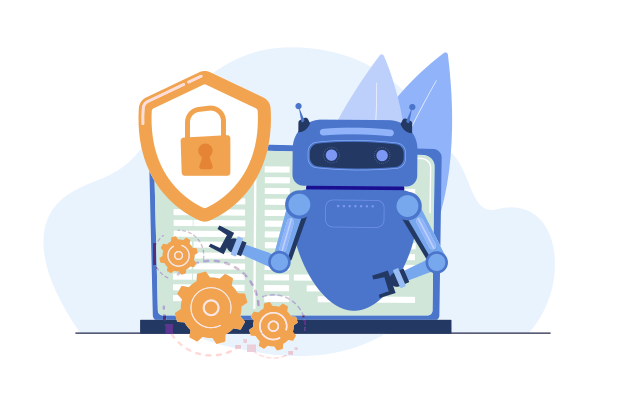
Today robots are used in many different areas and applications, and their safety-related problems have increased significantly. Each new area and application may call for specific precautions for operators, maintenance workers, robot systems, and so on. In the past, robot safety did not receive as much attention as it deserved from both manufacturers and users. This scenario is changing in recent years, and robot-related accidents could be one of the factors behind this change.
Source: Adapted from the chapter “Fundamentals of Robot Safety” (Dhillon 1991).
8.1 Reading: Workplace Robotics Safety
Many hazards and injuries can result from the use of robots in the workplace. Some robots, notably those in a traditional industrial environment, are fast and powerful. This increases the potential for injury as one swing from a robotic arm, for example, could cause serious bodily harm. There are additional risks when a robot malfunctions or is in need of maintenance. A worker who is working on the robot may be injured because a malfunctioning robot is typically unpredictable.
There are four types of accidents that can occur with robots. Impact or collision accidents occur generally from malfunctions and unpredicted changes. Crushing and trapping accidents occur when a part of a worker’s body becomes trapped or caught on robotic equipment. Mechanical part accidents can occur when a robot malfunctions and starts to “break down,” where the ejection of parts or exposed wire can cause serious injury. Other accidents at just general accidents that occur from working with robots.
There are seven sources of hazards that are associated with human interaction with robots and machines. Human errors could be anything from one line of incorrect code to a loose bolt on a robotic arm. Many hazards can stem from human-based error. Control errors are intrinsic and are usually not controllable nor predictable. Unauthorized access hazards occur when a person who is not familiar with the area enters the domain of a robot. Mechanical failures can happen at any time, and a faulty unit is usually unpredictable. Environmental sources are things such as electromagnetic or radio interference in the environment that can cause a robot to malfunction. Power systems are pneumatic, hydraulic, or electrical power sources; these power sources can malfunction and cause fires, leaks, or electrical shocks. Improper installation is fairly self-explanatory; a loose bolt or an exposed wire can lead to inherent hazards.
Emerging robotic technologies can reduce hazards to workers, but can also introduce new hazards. For example, robotic exoskeletons can be used in construction to reduce load to the spine, improve posture, and reduce fatigue; however, they can also increase chest pressure, limit mobility when moving out of the way of a falling object, and cause balance problems. For collaborative robots, isolation is not possible. Possible hazard controls include collision avoidance systems, and making the robot less stiff to lessen the impact force.
Source: Adapted from the Wikipedia article “Workplace robotics safety” (Wikipedia contributors 2021f), which is released under the Creative Commons Attribution-Share-Alike License 3.0.
Four types of accidents
- other accidents
Seven sources of hazards
- human errors
- control errors
- improper installation
Show/Hide solution
1.impact or collision; 2.crushing and trapping 3.mechanical part
3.unauthorized access; 4.mechanical failures; 5.environmental sources; 6.power systemsShow/Hide solution
chest pressure, limit mobility, balance problems8.2 Writing: What is a Robot Safety Standard?
Use the following words to fill in the blanks.
international; safe operations; organizations; safety standard; global market
Source: Adapted from the article “Robot Safety Standards: A Brief Overview” (Robotics Online 2017).
A robot
Some common standards
- American National Standards Institute (ANSI)
- U.S. Standards Body including CSA, BSI, DIN, AFNOR, JISC and more
- International Organization for Standardization (ISO)
- International Standards Body
- International Electrotechnical Commission (IEC)
- International Standards Body
Much of the work of robot safety standards organizations is involved in making
Show/Hide solution
safety standard; safe operations; organizations; international; global market8.3 Speaking: Who Is At Fault? Who is Liable?
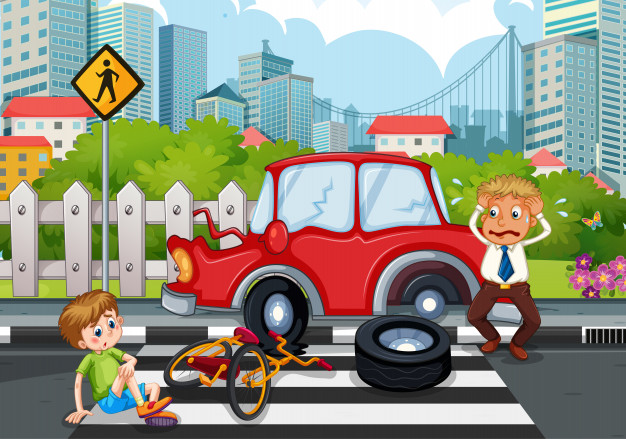
8.4 Listening: Collaborative Robot - Risk Assessment
In a
Evaluating a risk correctly can be a game-changer in your risk assessment process.
The risk is usually evaluated using four different criteria: severity of injury, possibility of occurrence, possibility of avoidance, and
Let’s take the simple example of a gripper hitting my hand against the table.
The severity of injury is rated from 0.25 to 0.65. The lowest being a scratch or a bruise. The highest being
The second
The third criterion is possibility of avoidance rated from possible being 0.75 to impossible being 5. In this case the robot is not moving fast enough to
Finally, the frequency of exposure is rated from 0.5 being annually to 5 being constantly. In this case, the worker is exposed daily to the answer.
Then all these criteria are multiplied together to give a certain rate. In this case 1.4 which is considered as being
Once all your risks are evaluated. You can do a risk reduction process starting with the most dangerous one.
Show/Hide solution
risk assessment; frequency of exposure; catastrophic; criterion; crush; neglectable8.5 My Glossary
Translate these terms into your language.